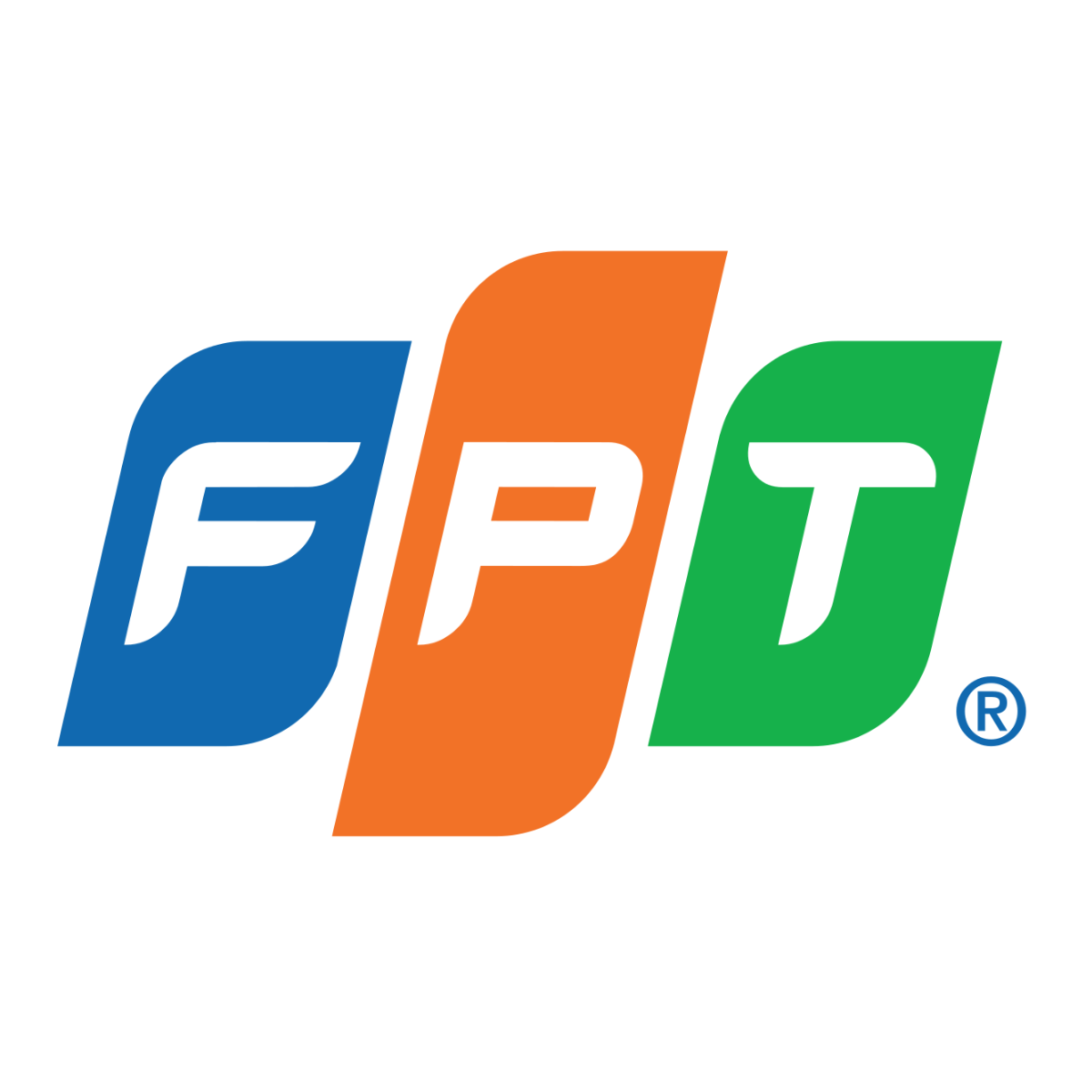
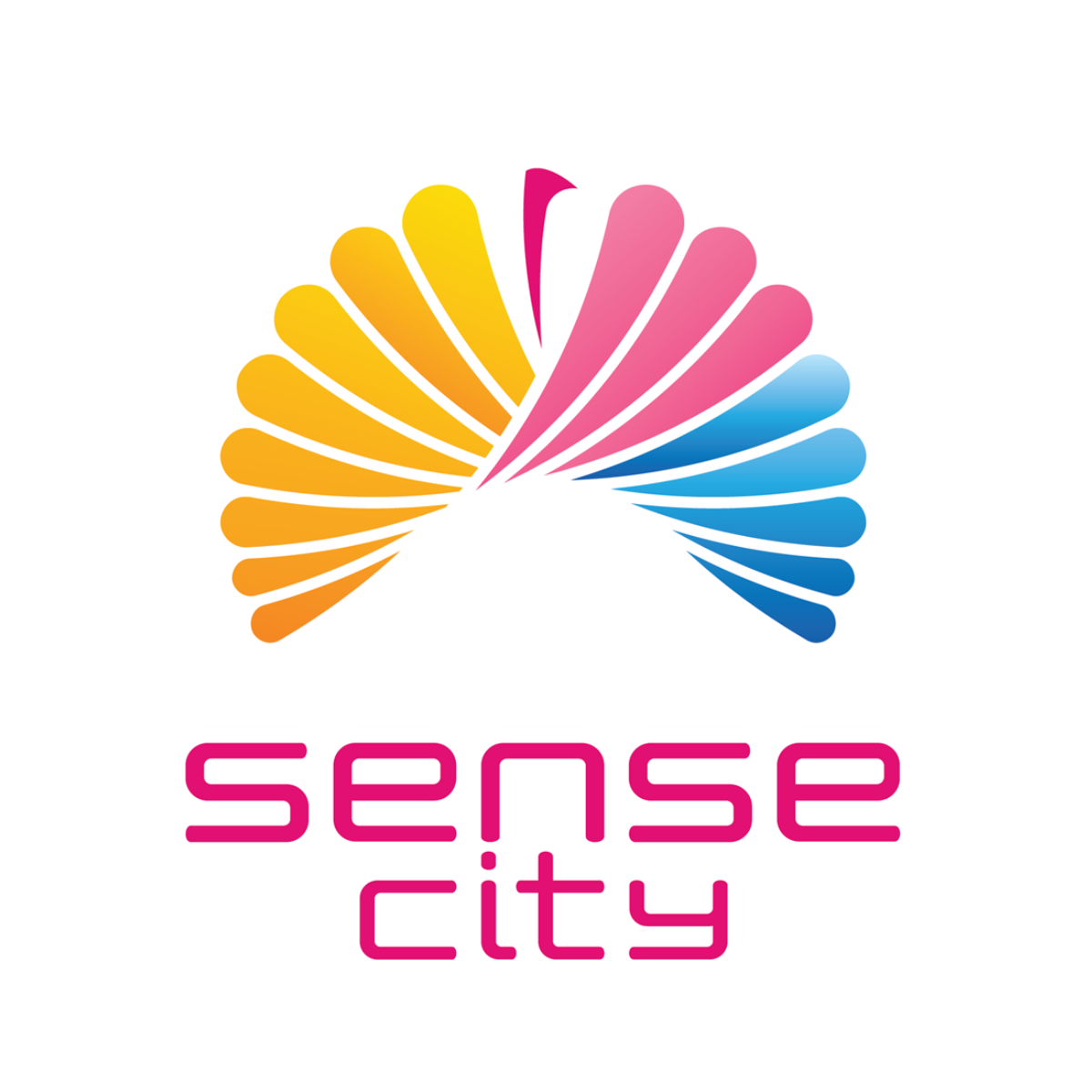
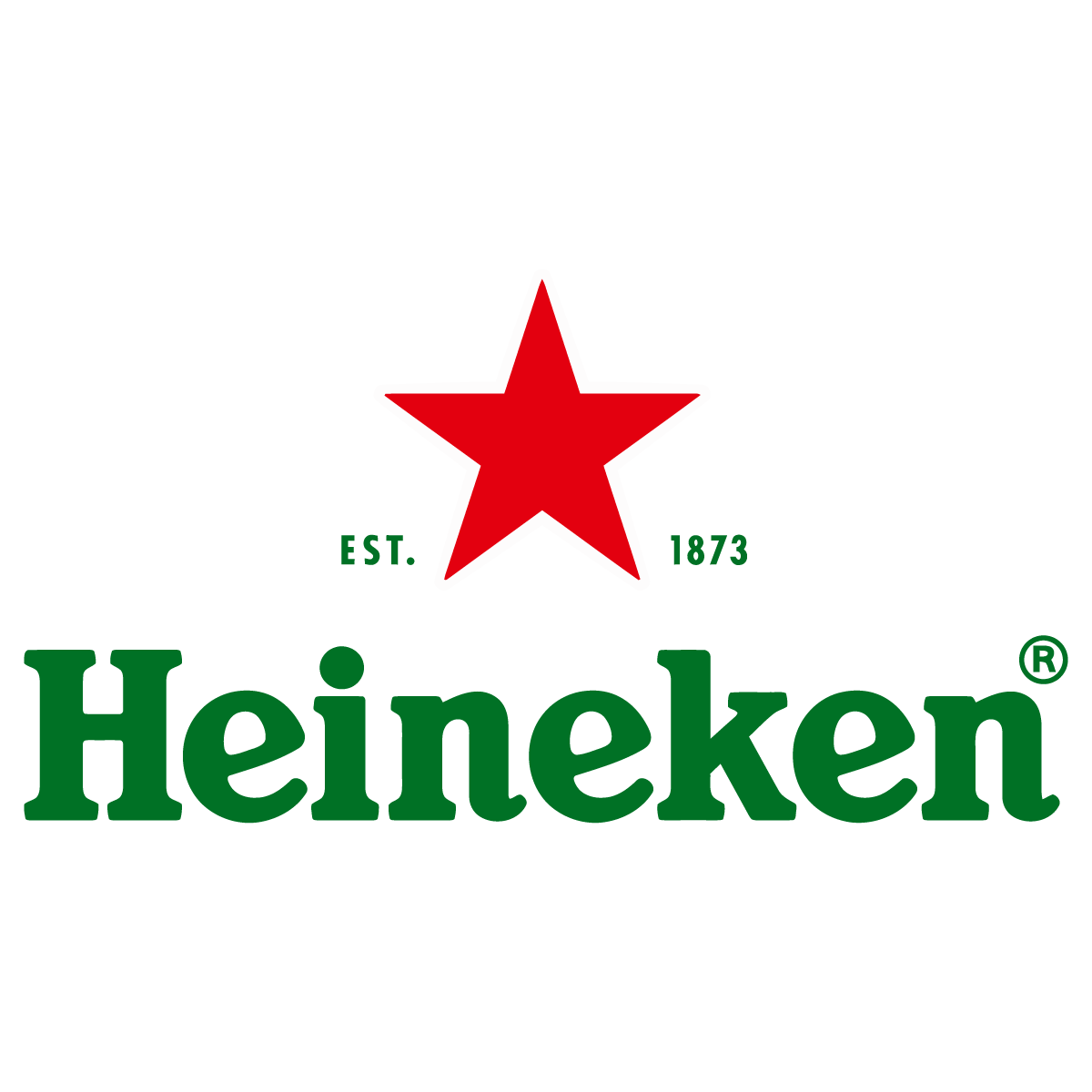
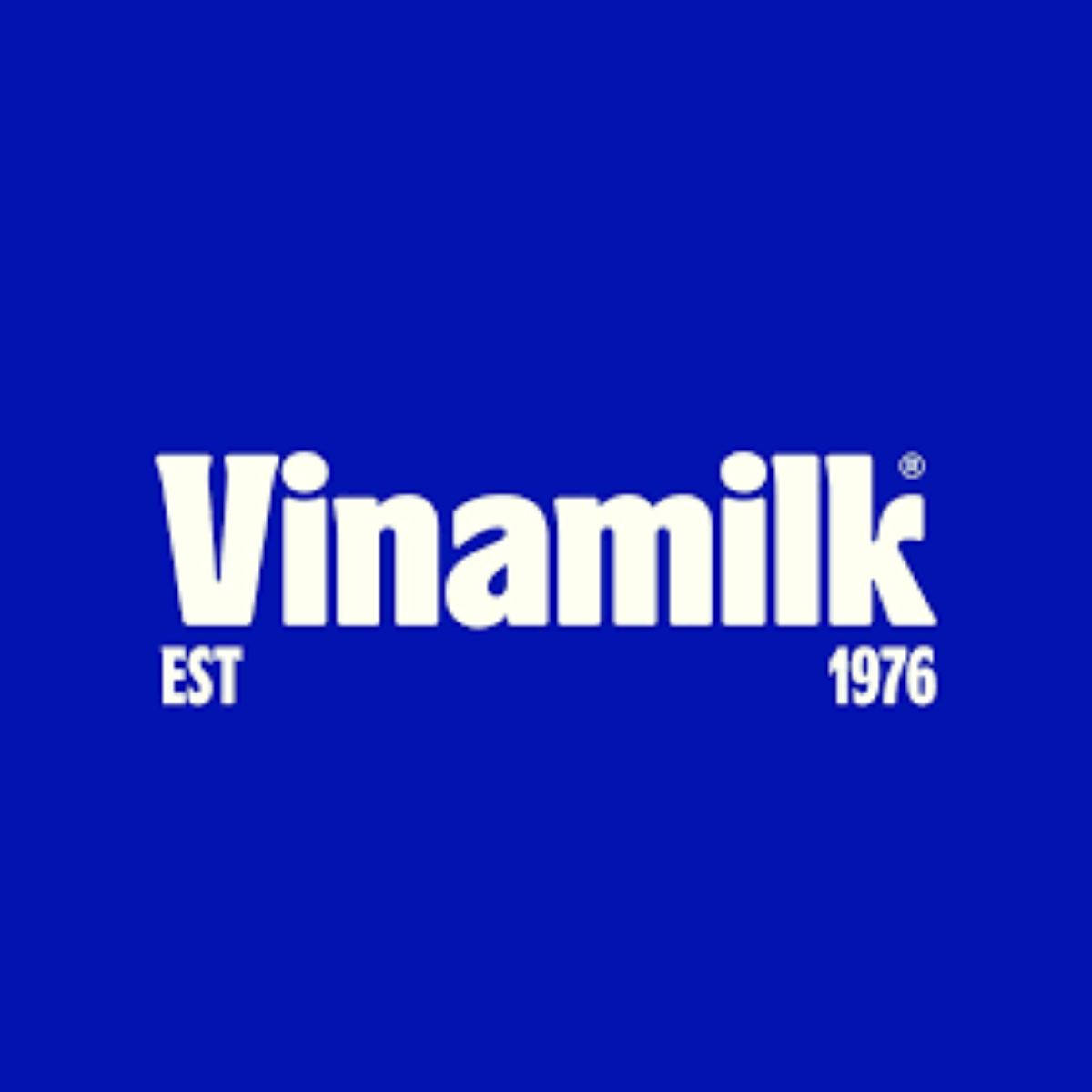
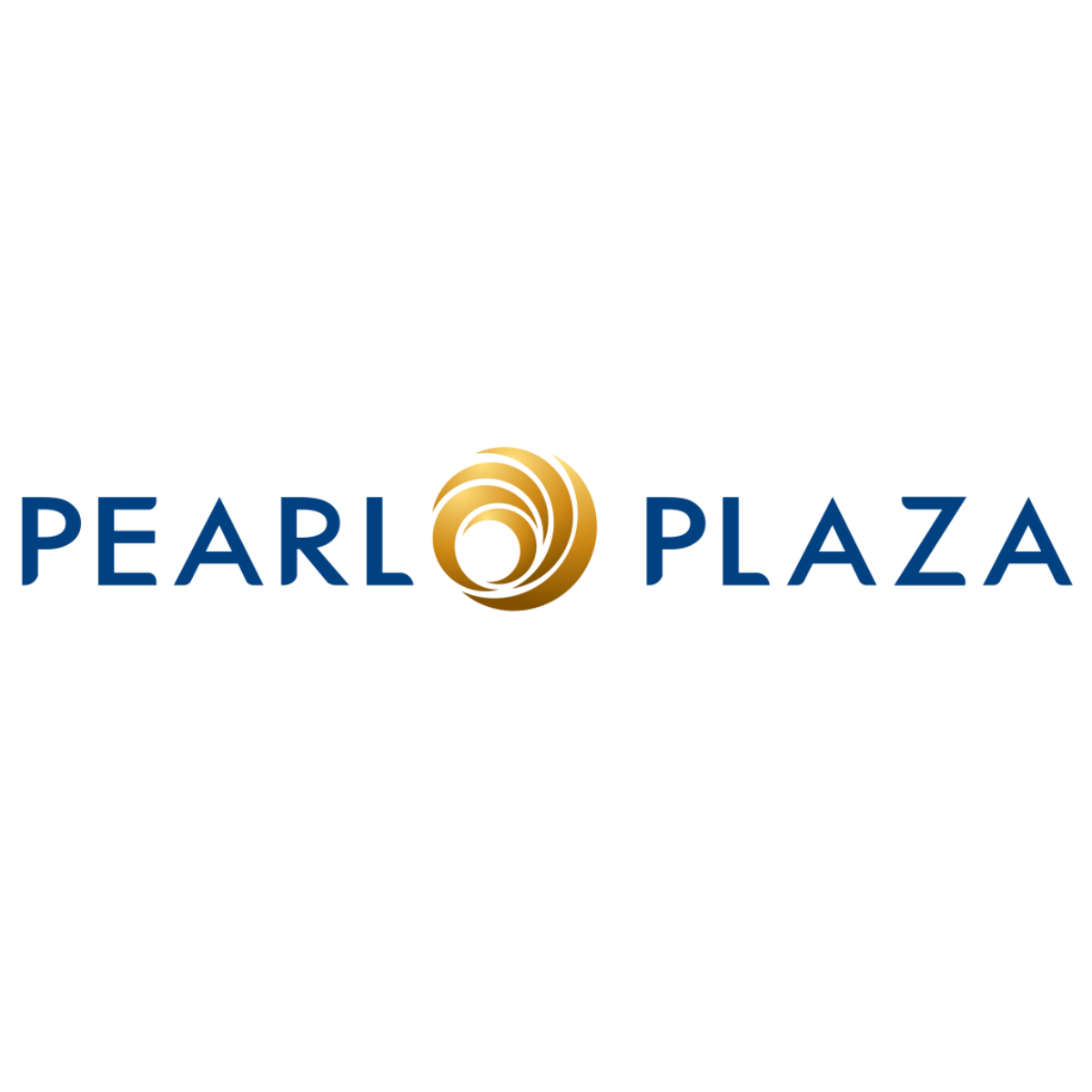
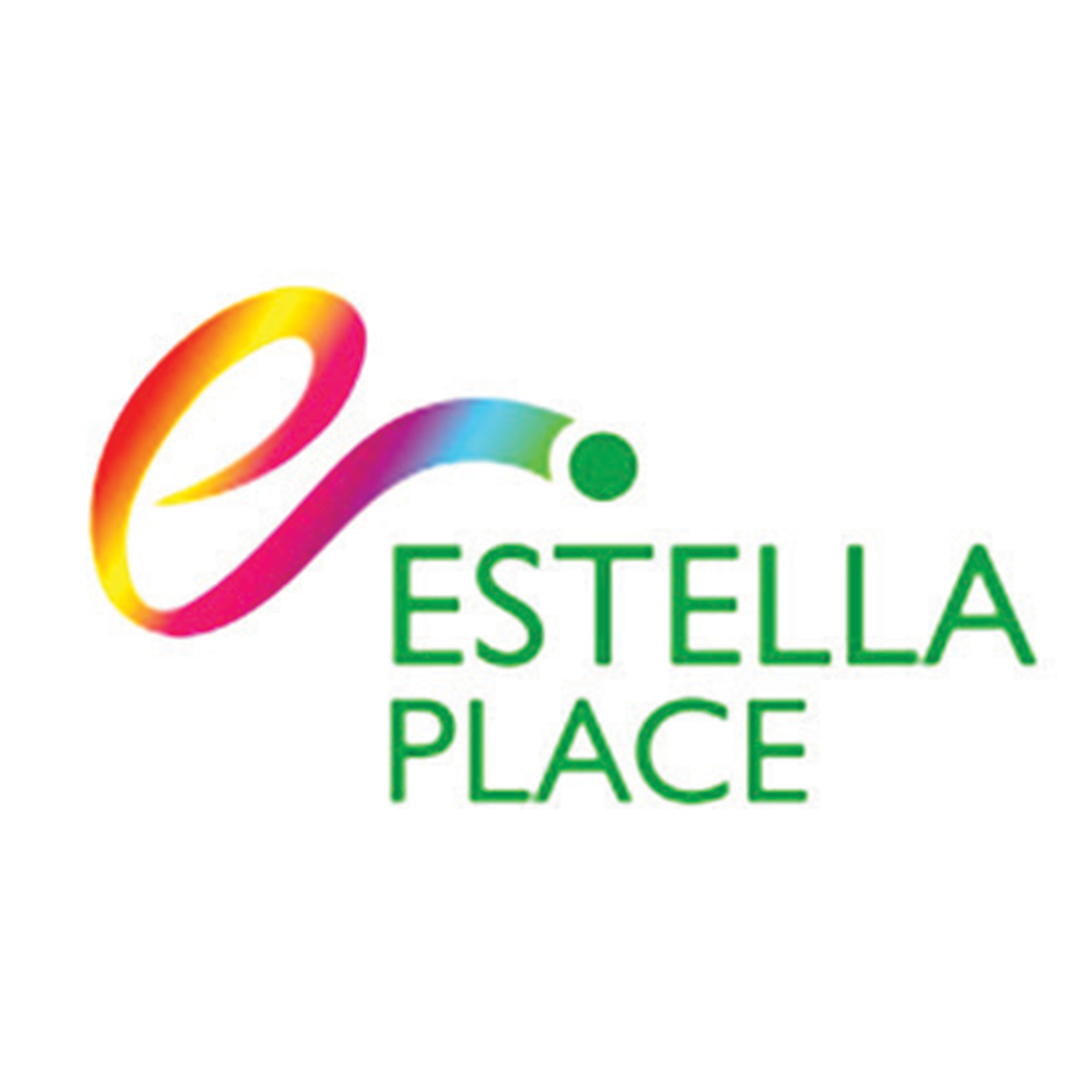
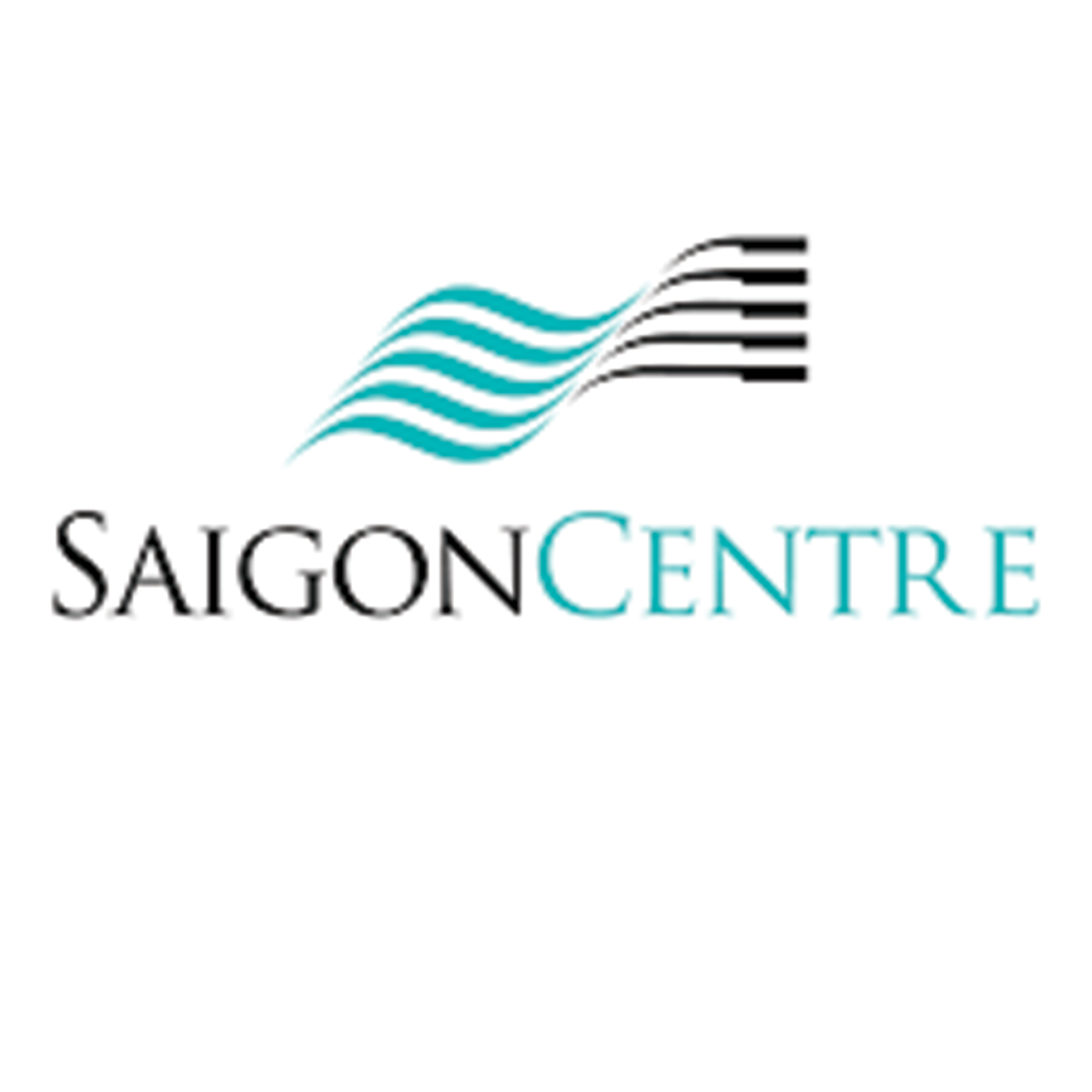
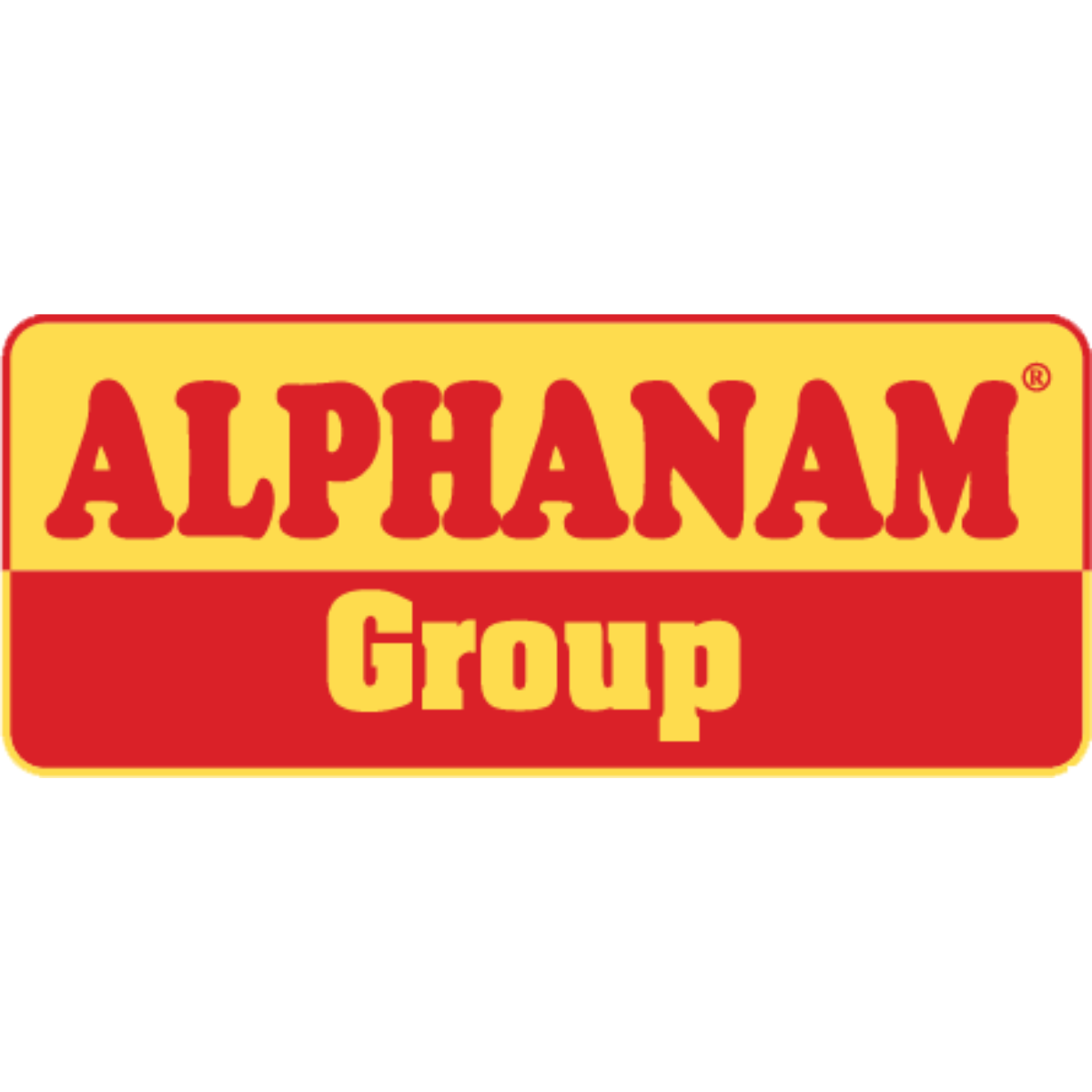
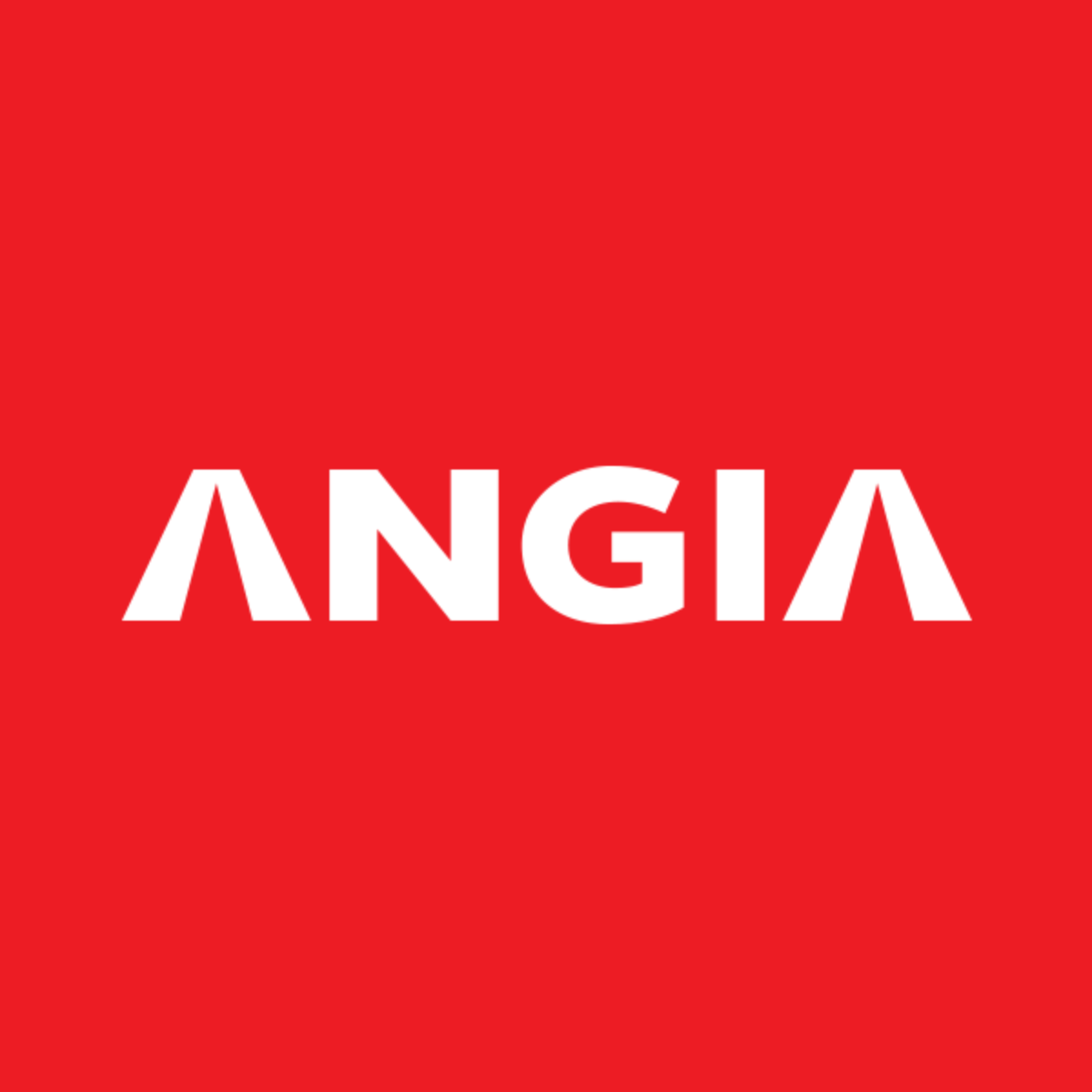
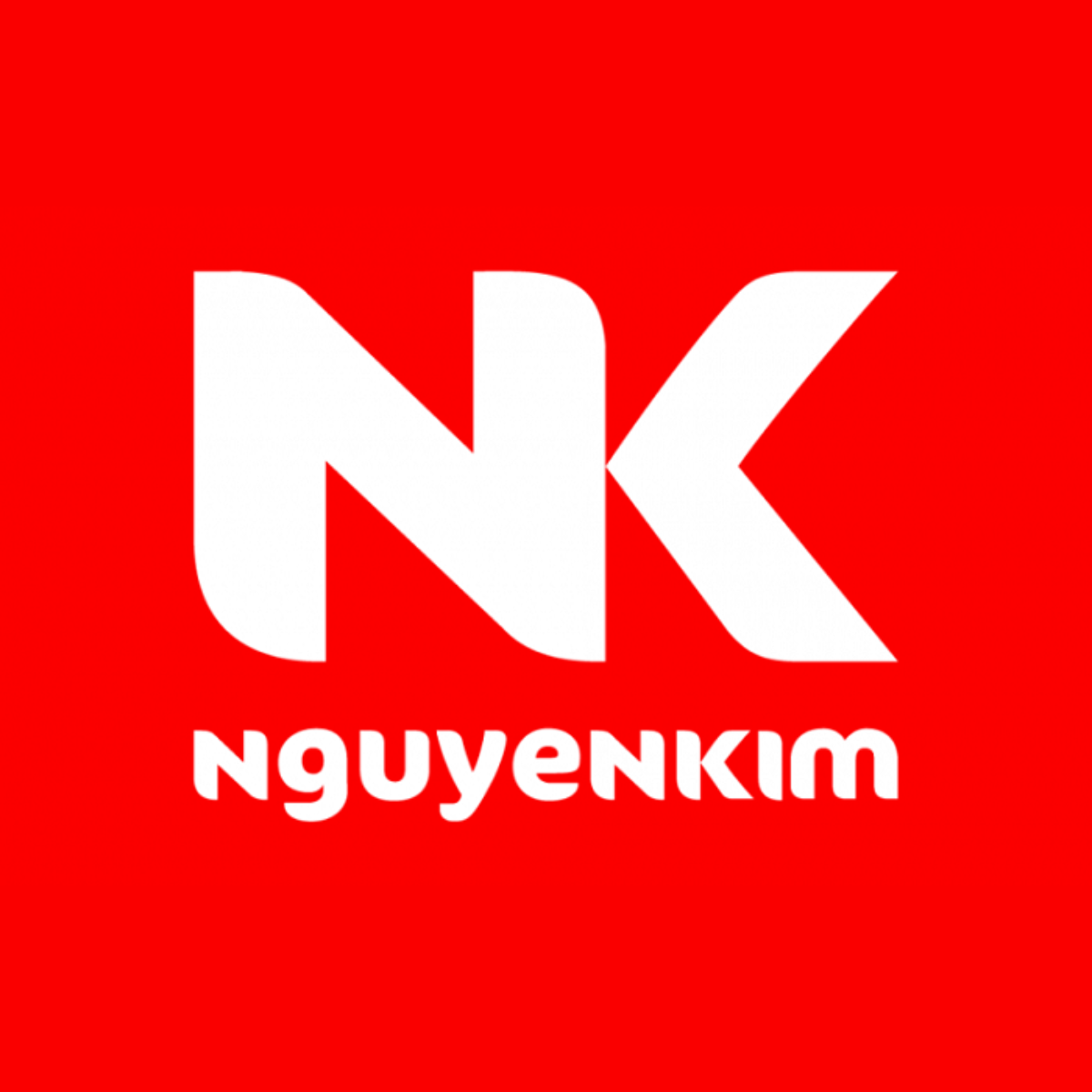
The PDCA process (also known as the Deming Cycle) is a cycle of monitoring and changing or setting goals that consist of the elements Plan (P)-Do (D)-Check (C) and Act (A). PDCA was initially introduced as a sequential management work step to maintain existing quality. This is now one of the essential processes in quality management systems such as ISO 9001, ISO 14001, and others.…
Quy trình PDCA
We are proud to be a forerunner foreign enterprise in the fields of smart parking management, security, and smart home systems. TSP has used the PDCA process to improve service quality for customers.
When TSP takes over a project, this is the first and most important step. We always construct the plan in the most meticulous and detailed manner possible. Meeting the customer's requirements while minimising risks that may arise during the implementation process..
TSP's technical staff will carry out a detailed implementation of the planned workload after defining the tasks and standardising the methods. Furthermore, TSP's staff is outfitted with cutting-edge equipment and machinery, allowing for quick resolution of issues that arise during the implementation process. Measure and monitor the work on a regular basis to ensure that the schedule is kept as committed to the customer.
In quality management, it is indispensable to check the performance results. Before handing over the system, it must be perfected by detecting inappropriate points and errors and providing appropriate solutions.
There will be appropriate assessments and impacts based on the evaluation results to adjust, overcome, and improve the service.
TSP uses the PDCA process in quality management, as well as ERP in human resource management, modern technologies, and diversified solutions to meet the needs of each customer, including commercial centres, buildings, supermarkets, urban areas, high-class apartments, factories, hospitals, and schools.
...........................................
Contact information:
TSP
Address: G Floor, Rosana Tower – 60 Nguyen Dinh Chieu St., Dakao W., Dist. 1, HCMC
Hotline: 0909 411 885
Linkedin: https://www.linkedin.com/company/taiseismartparking/
Facebook: https://www.facebook.com/tsp.com.vn